Comment bien gérer mes batteries?
sur
Qu'y a-t-il de si particulier dans les piles au lithium ? Pourquoi leur faut-il, contrairement aux autres techniques de stockage courantes, une gestion électronique de la charge des batteries ? Cet article répond à ces questions.
Sans lithium
Plomb
Tout était si simple avec les batteries au plomb : vous injectez dans la batterie autant de courant que possible et vous arrêtez dès que la tension de fin de charge (que nous appellerons ici TFC, pour seuil de tension de fin de charge) est atteinte. Quant aux batteries composées de plusieurs cellules (en série), il suffit de multiplier leur TFC par le nombre de cellules et le tour est joué. Ça marche encore aujourd'hui, parce que les batteries au plomb supportent une certaine surcharge, en émettant tout au plus un peu de gaz. Si la capacité de l'une des cellules d'une batterie est inférieure au reste, rien ne vous empêche de charger toutes les cellules jusqu’au même seuil TFC. Pour transporter un ordinateur portable équipé de batteries au plomb, il faudrait un chariot. Il a donc fallu trouver autre chose. Dans l’automobile en revanche, leur robustesse explique que presque toutes les autos restent équipées d'une anachronique batterie de 12 V au plomb, alors que d'autres types de batteries permettraient d'alléger le véhicule. Ces batteries sont si robustes qu'une batterie de (petite) voiture standard de 44 Ah résiste vaillamment pendant des années aux tortures infligées par un alternateur de 55 A et un régulateur rudimentaire. C’est assez impressionnant.
La tension nominale d'une cellule est de 2 V. La TFC est d'environ 2,35 à 2,4 V/cellule, soit 14,1 à 14,4 V pour la batterie de voiture à six éléments. Une cellule de batterie au plomb ne doit pas être déchargée en dessous de 1,8 V. Une batterie de voiture sera donc endommagée si sa tension passe sous le seuil de 10,8 V, comme cela peut arriver avec une autodécharge d'environ 5 %/mois. Le motard en hibernation connait bien ce problème saisonnier.
Nickel-Cadmium
Les piles rondes dites NiCd sont devenues populaires comme remplaçantes des piles zinc-carbone dans les appareils de grande consommation. Ce type de pile est interdit dans l'UE depuis plus de 10 ans en raison de la nocivité du cadmium. Les batteries NiCd ont maintenant disparu de la vie quotidienne.
Voici en bref leurs caractéristiques : les batteries NiCd tolèrent des courants d’assez forte intensité et de nombreux cycles de charge. Elles étaient souvent utilisées pour les modèles réduits de voitures, etc. Leur tension nominale est de 1,2 V par cellule. La charge est similaire à celle des batteries au plomb-acide jusqu'à des seuils TFC de 1,5 à 1,57 V/cellule (en fonction du courant). Une décharge profonde en dessous de 0,85 V/cellule endommage la batterie, même si celle-ci reste globalement beaucoup plus robuste qu'une batterie NiMH ou au lithium. L'autodécharge peut atteindre 20 % par mois. Pour la charge, la connexion en série de plusieurs batteries ne pose aucun problème.
Nickel-hydrure métallique
Les petites piles rondes NiMH, telles que le type AA (fig. 1) se sont substituées aux piles NiCd comme alternative non toxique.
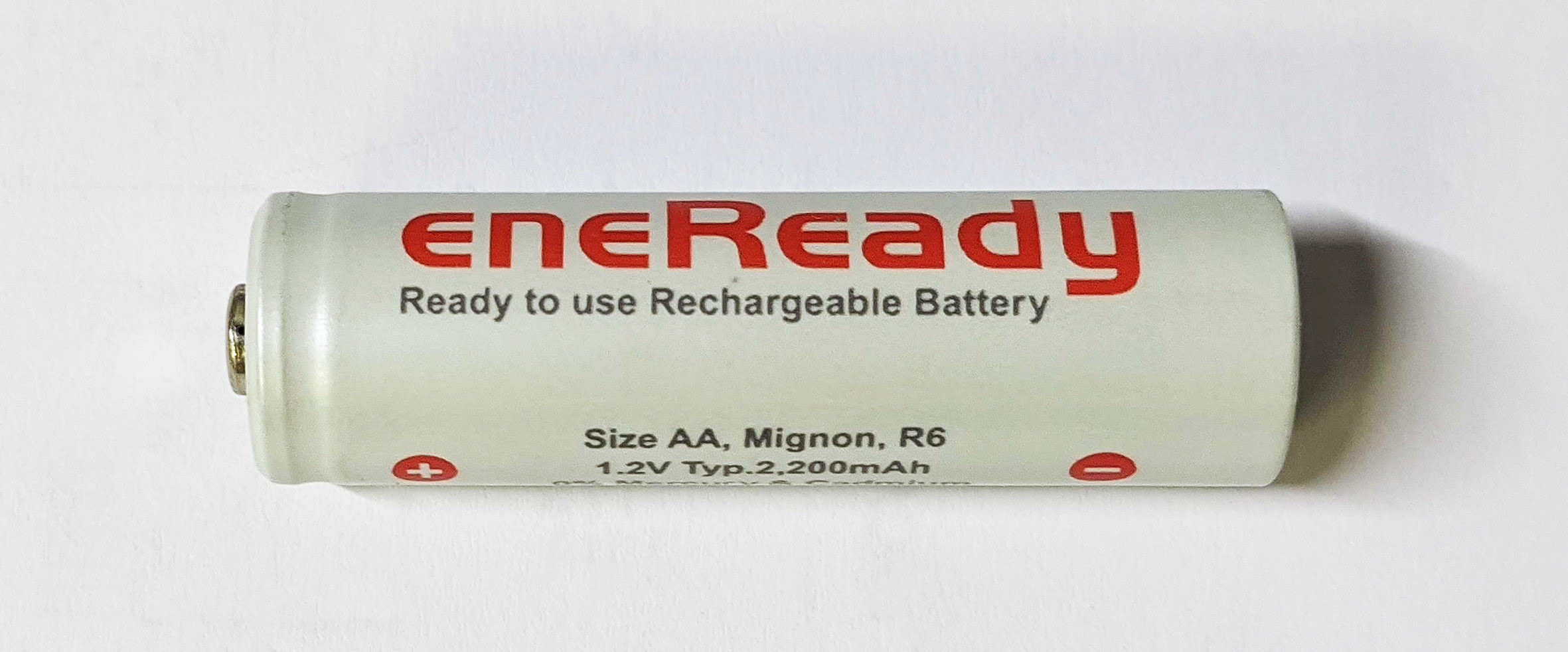
Elles sont disponibles en petites tailles, depuis des années dans les outils à piles p. ex. grâce leur prix bas et leur maniement facile. Il en existe aussi des modèles plus grands : le prototype de toutes les voitures hybrides, la Toyota Prius, était équipé sur les modèles II et III d'une batterie NiMH de près de cent livres, d'environ 200 V et d'environ 6,5 Ah. Sur ces voitures, cette batterie atteint des durées de vie et des nombres de cycles inouïs grâce à la gestion du comportement de charge et de décharge, et à l'utilisation d'une capacité partielle seulement. La figure 2 montre la batterie ouverte de mon ancienne Prius II.
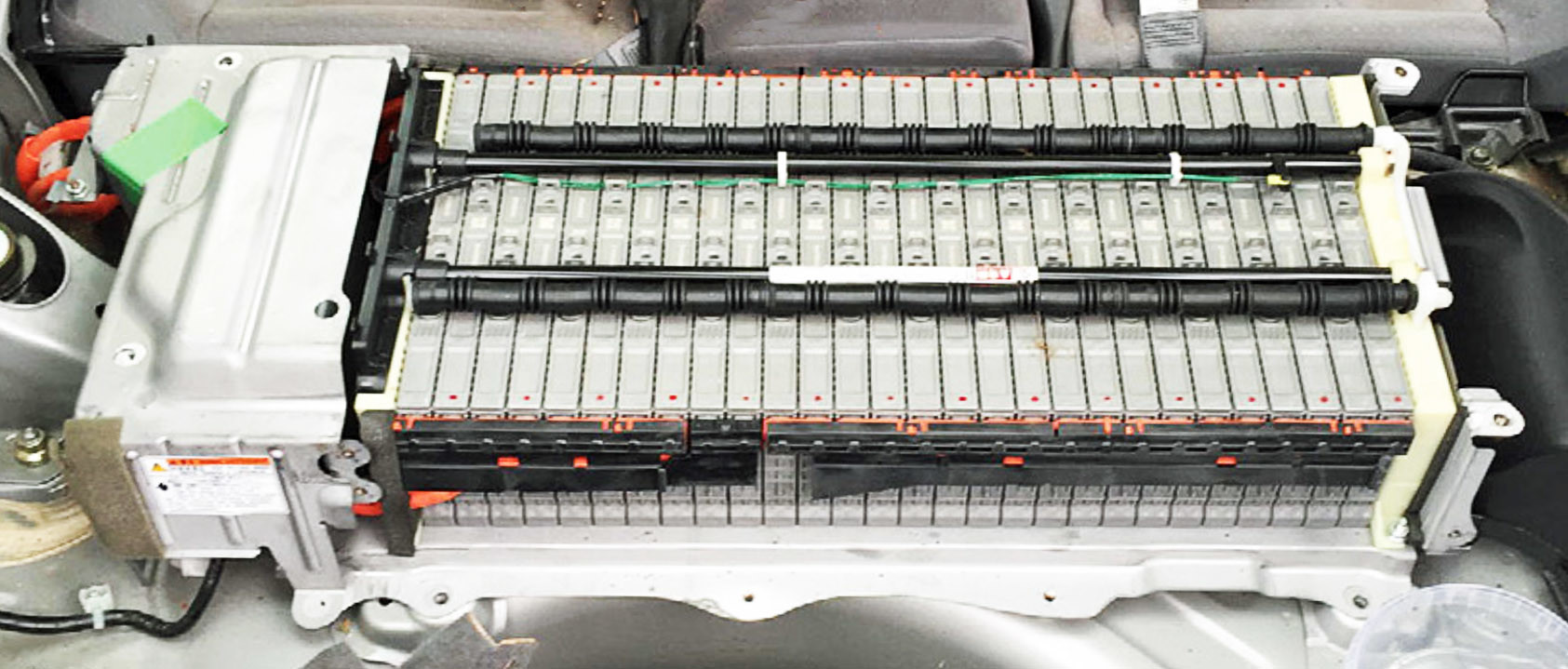
Une fois (suffisamment bien) résolus les problèmes liés à cette technique, Toyota et tous les autres fabricants sont passés au lithium pour leurs hybrides rechargeables et leurs modèles hybrides plus récents, en raison des économies de poids.
L'autodécharge des batteries NiMH est (en principe) similaire à celle des NiCd. En pratique, il existe cependant des variantes telles que la batterie de la figure 1, avec un taux d'autodécharge beaucoup plus faible, d'environ 1,5 %/mois, au détriment de la densité de puissance. Pour les petits appareils moins fréquemment utilisés, de telles piles sont toujours préférables, car les piles NiMH profondément déchargées deviennent inutilisables.
Lithium
Les piles à base de lithium prennent peu à peu toute la place, du fait de leurs meilleures performances (puissance, poids) et de leur faible autodécharge, de l’ordre de 5 %/an. Il n’y a pas de lumière sans ombre : les batteries dites li-ion (lithium-ion) sont très sensibles à la surcharge et à la décharge profonde. Non seulement elles perdent de leur capacité, mais certains types peuvent éclater ou prendre feu. À basse température, la capacité disponible diminue. Le phénomène est réversible, mais reste problématique sur les voitures électriques. Les batteries au li-ion ne supportent pas bien non plus les températures élevées.
En raison de la sensibilité à la surcharge, il convient de surveiller les tensions lors de la connexion en série. En tout état de cause, il faut ici un "équilibreur" supplémentaire (balancer en anglais), qui empêche la surcharge de certaines cellules dont la capacité serait par hasard un peu plus faible, tandis que d’autres cellules ne seraient pas encore complètement chargées. Et ce n’est pas tout. Les batteries li-ion nécessitent toujours un système de gestion de batterie (BMS pour battery management system) aux caractéristiques parfois complexes.
Ce qui complique encore le sujet, c'est la diversité des types de batteries au lithium. En fonction de la technologie utilisée et de la chimie interne, le nombre de cycles possibles, la TNC (pour tension nominale de cellule), la TFC, la TFD (pour tension de fin de décharge), le courant de décharge maximal et d'autres paramètres varient. Le BMS doit être adapté à ces paramètres et bien sûr aux courants et aux conditions de température à contrôler dans le cas spécifique.
En dehors des voitures électriques, pour lesquelles des conditions spéciales s'appliquent et dans lesquelles d'énormes efforts sont faits pour protéger les batteries coûteuses, c’est heureusement un peu plus facile avec les systèmes de batteries plus petits, par exemple pour les appareils portables tels que les ordinateurs portables ou les HP Bluetooth, les outils tels que les tournevis sans fil ou les appareils ménagers tels que les aspirateurs sans fil, car le refroidissement et le chauffage ne sont pas nécessaires. D'ailleurs, le plus simple est de le faire avec des smartphones, car ils ne contiennent pas de piles connectées en série, ce qui explique pourquoi aucun équilibreur n'est nécessaire. L'électronique de charge intégrée ne doit prendre en compte que la TFC et la TFD ainsi que le courant de charge maximal.
Parmi les petites piles li-ion, deux catégories dominent : il existe des types dont les électrodes sont construites avec les matériaux suivants : cobalt, dioxyde de cobalt, manganèse et/ou nickel et aluminium. La technologie LiCoO2, qui a fait ses preuves, se taille la part du lion dans ce domaine. Heureusement pour tous ces types, la TNC est d'environ 3,6 à 3,7 V, la TFC de 4,2 V et la TFD de 2,5 V (à l’exception du LiNixCoyAlzO2, dont la TFD est de 3,0V). Même si les courants autorisés et la durée de vie sont différents, tous ces types peuvent en principe être gérés avec les mêmes procédures et donc les mêmes circuits intégrés.
La batterie est composée de phosphate de fer et de lithium (LiFePO4), avec les caractéristiques suivantes : TNC = 3,2 V, TFC = 3,65 V et TFD = 2,5 V. Ce type de batterie offre un nombre de cycles élevé et une densité de puissance légèrement inférieure . Il faut donc des équilibreurs au moins pour ces tensions. L'industrie des semi-conducteurs propose bien sûr des solutions pour les deux catégories et pour divers nombres de cellules et courants connectés en série – certains circuits intégrés sont même programmables, commutables pour certains paramètres ou possèdent une interface pour les microcontrôleurs.
Les piles li-ion sont disponibles en plusieurs modèles : Les types li-po (lithium polymère) sont principalement utilisés dans les appareils mobiles et les ordinateurs portables en raison de leurs formes possibles et de leur planéité. Le terme polymère rappelle simplement que les li-po sont scellées dans un film de plastique au lieu d'un boîtier rigide (ne pas couder !). Il y a ensuite diverses cellules rondes, dont le type particulièrement courant 18650 (ø = 18 mm, longueur = 65 mm), qui, chose étonnante, est installé par milliers en paquets dans les voitures électriques Tesla – l’espace entre les cellules rondes sert à réguler la température. La fig. 3 montre une cellule 18650 provenant de la production chinoise avec des spécifications fantaisistes : sur papier tout comme sur le plastique et en HTML, on peut dire n’importe quoi : 7 800 mAh ne correspondent pas, et de loin, au format de la cellule 18650.
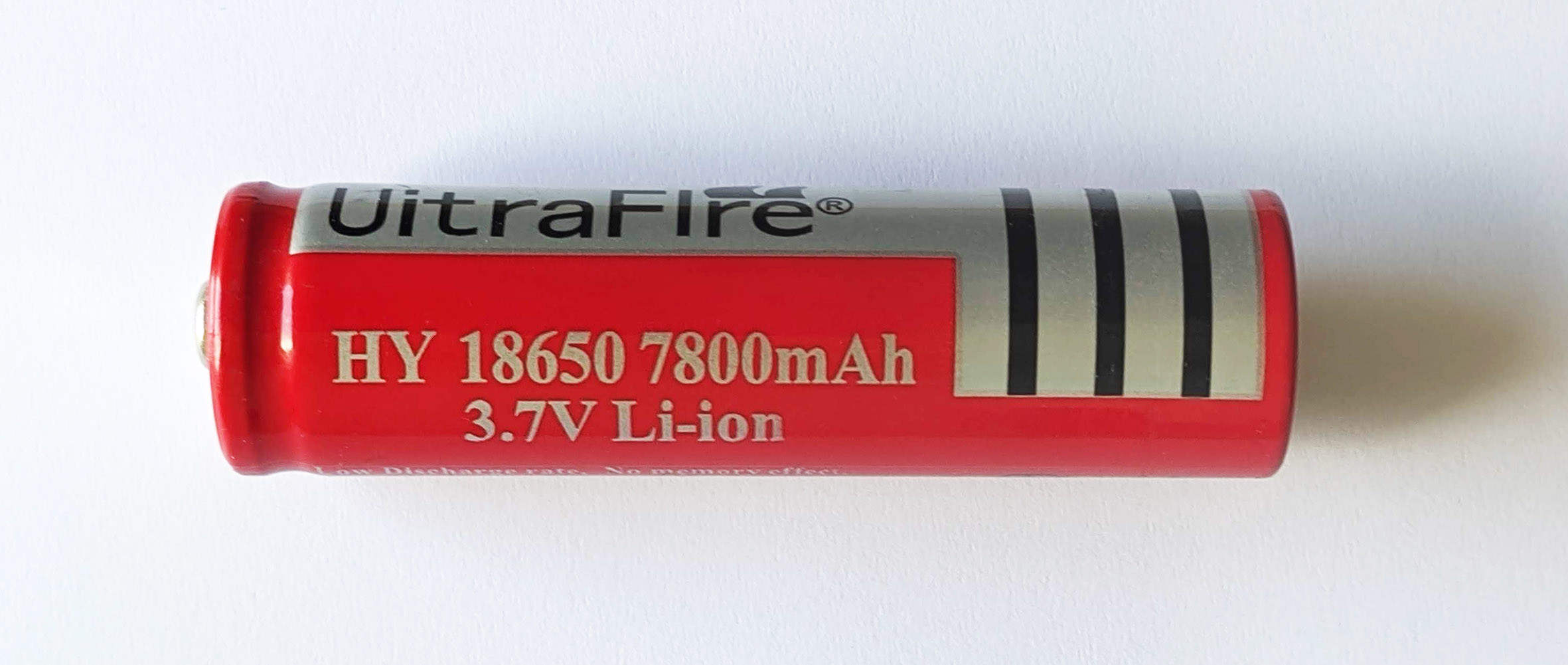
Les meilleures cellules sont environ deux fois plus petites en termes réels. Enfin, il y a les cellules dites prismatiques, dont la désignation indique simplement que leur logement n'est pas rond mais prismatique. De telles cellules sont par exemple utilisées dans la mini voiture Hotzenblitz de production allemande. La fig. 4 montre que chaque cellule est équipée d'un système électronique supplémentaire de surveillance.
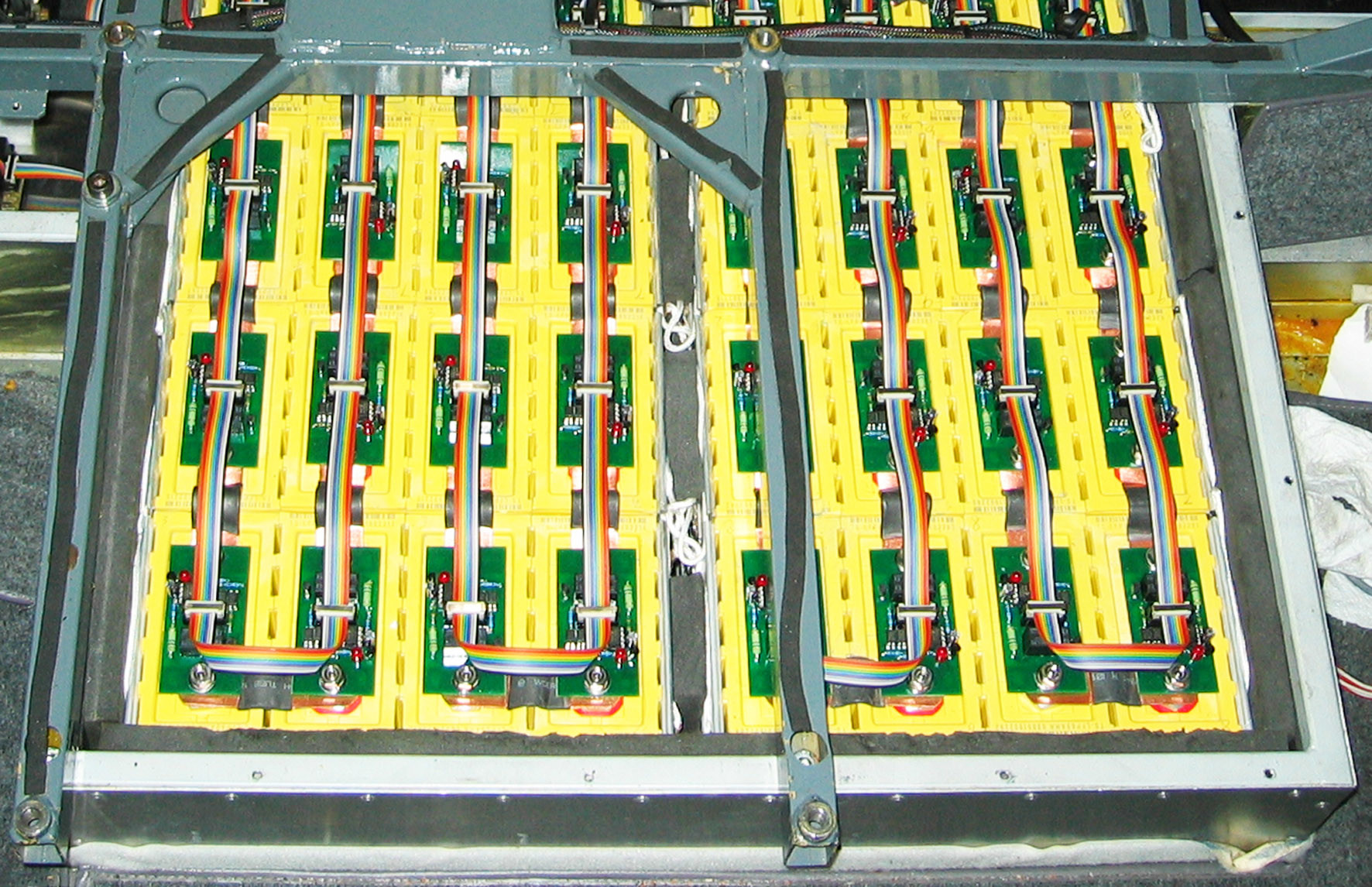
Équilibreur
La notion de gestion de la batterie est assez vague. Elle englobe tout ce qui concerne de près ou de loin la surveillance et le contrôle de la charge, de la décharge et de l'état de fonctionnement des batteries. Alors que dans le cas des batteries plomb-acide, NiCd et NiMH, cela ne concerne que la conformité avec les TFC, TFD et, occasionnellement, la limitation des courants, la question est plus complexe en raison des problèmes de connexion en série des cellules de batteries au lithium. Dans ce cas, le BMS a nécessairement besoin d'un équilibreur s'il y a plus d'une cellule !
Les piles au lithium n'aiment pas la surcharge. Et comme la capacité des cellules d’un même lot varie légèrement, même en cas de production de masse, et que des différences peuvent également apparaître au fil du vieillissement, il y aura toujours, dans une connexion en série, une cellule pleinement chargée avant les autres. À ce stade, cependant, la TFC pour l'ensemble de la batterie n'est pas encore atteinte, et si la charge devait se poursuivre, la cellule déjà chargée serait forcément endommagée – lors de la prochaine charge, elle serait "prête" encore plus tôt ; après quelques cycles, ce cercle vicieux conduirait à une défaillance totale de cette cellule et donc de la batterie entière. Un équilibreur a pour vocation d'éviter cela.
Dans la version la plus simple pour une batterie à deux cellules (fig. 5), l'équilibreur surveille les tensions des deux cellules.

Si l'une des deux cellules atteint le seuil TFC, une charge faible appropriée est ajouté en parallèle avec cette cellule, de sorte que le courant de charge excédentaire passe ne passe pas dans cette cellule, mais à côté, et que l'autre cellule, dont la capacité est meilleure, puisse encore être chargée entièrement. Avec plus de cellules, l'équilibreur sera dimensionné en conséquence. Le petit tableau (fig. 6) montre un BMS pour quatre (petites) cellules proposées sur eBay pour différents nombres de cellules à des prix compris entre 1 € et 10 €.
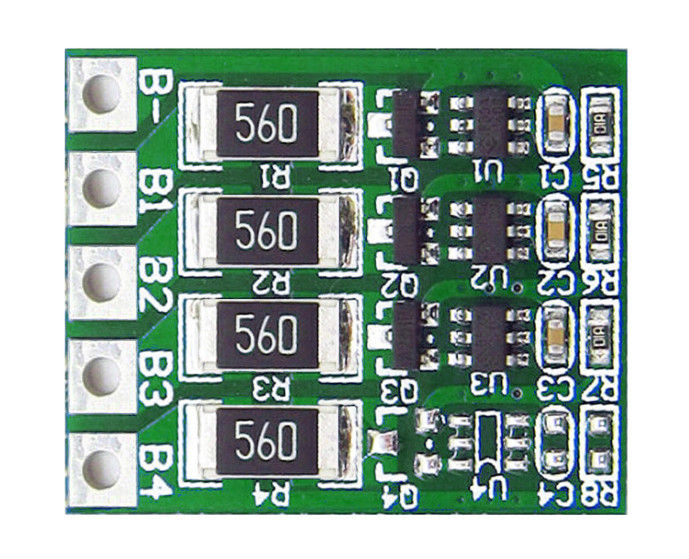
La fig. 7 rend compte de mes efforts pour équilibrer la batterie LiFePo 48 V de mon clone Segway : chaque cellule est surveillée par son propre microcontrôleur.
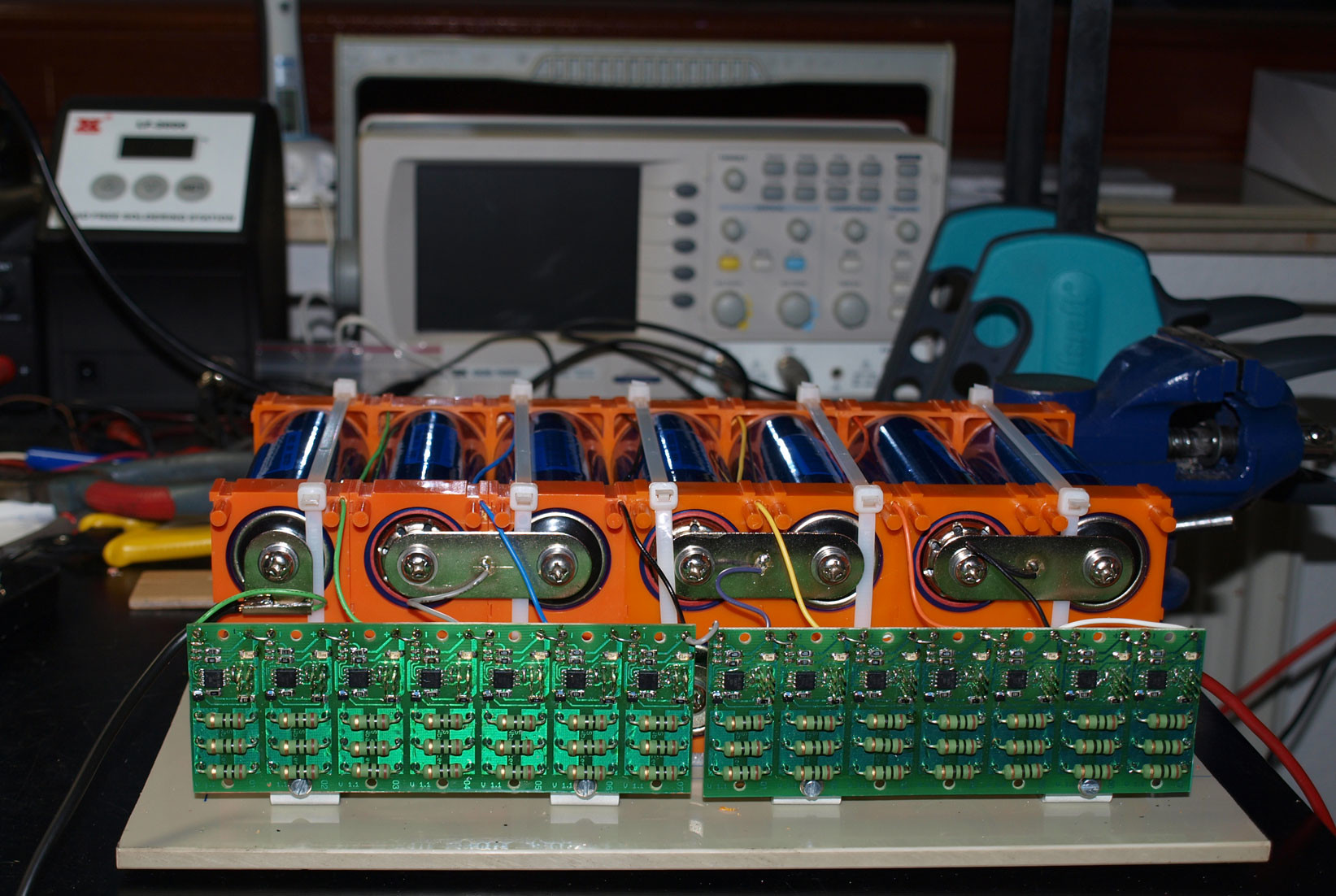
Ça paraît lourd en théorie, mais pas en pratique. En termes purement formels, la charge connectée en parallèle en cas d'urgence devrait pouvoir faire passer en douce le courant de charge complet en dehors de la cellule à protéger, mais dans la pratique, ce courant est bien inférieur au courant de charge maximum susceptible de circuler. La raison en est que les batteries li-ion sont initialement chargées avec le courant nominal jusqu'à un état de charge de 50 à 80%, mais à partir de là, seulement avec un faible courant, généralement en diminution constante. Avec les piles LiCoO2, pendant la charge, le courant est assez faible au-delà de 3,95 V. Comme les différences entre cellules saines ne sont pas si grandes, il suffit de décharger ce courant beaucoup plus faible. En pratique, des charges supplémentaires pour environ 1 à 5 % du courant maximal sont presque toujours suffisantes. Si cela ne suffit pas, la cellule est défectueuse et un ballast plus élevé ne serait pas utile à long terme.
Selon les courants qui circulent, un équilibreur gaspille une énergie qu’il serait préférable d’utiliser. Il existe pour cela des équilibreurs spéciaux qui ne convertissent pas simplement en chaleur l'énergie excédentaire de la cellule à protéger, mais la réinjectent directement dans le système global par le biais de régulateurs à découpage (par cellule !). Il serait surprenant toutefois que vous rencontriez souvent un tel souci du minuscule.
Un autre critère important : les équilibreurs sont basés sur des composants électroniques et le choix de circuits intégrés bon marché pour hautes tensions est limité. Par conséquent, les possibilités de mise à l'échelle butent sur des limites pratiques. Les circuits intégrés modernes de BMS sont généralement disponibles pour 2 à 12 cellules. Avec 12 cellules, vous avez déjà une tension de fonctionnement d'environ 50 V. Si vous voulez plus de cellules dans une batterie, il vous suffit de mettre à l'échelle l'électronique du BMS. Avec les systèmes sous 800 V des voitures électriques modernes, ça vous fera une vingtaine de modules avec des BMS-IC 12s en série (le "s" après 12 correspond à "cellule"). Les différents sous-systèmes sont ensuite reliés entre eux par un bus (isolé électriquement) et généralement à un système de commande central.
Circuits intégrés
Il existe une grande variété de circuits intégrés spéciaux pour toutes les applications imaginables – trop nombreux pour espérer en donner un aperçu utile ici. Au lieu de cela, nous décrirons un circuit intégré précis en guise d’exemple. Avant cela, précisons qu’en plus de l'équilibrage, un BMS a également pour tâche, dans la plupart des applications avec des batteries au lithium, de protéger la batterie contre les sous-tensions et les surintensités. Parfois, le circuit de charge est également inclus dans le système. Pour ces tâches complexes, l'utilisation d'un microcontrôleur tombe sous le sens. Les BMS modernes ont donc parfois un petit SoC intégré ou une interface équivalente. Les circuits intégrés de BMS ne figurent donc pas seulement au catalogue des fournisseurs habituels de circuits analogiques ou de régulateurs à découpage, mais aussi à celui d’entreprises telles que Microchip, Maxim (fig. 8) ou Renesas.
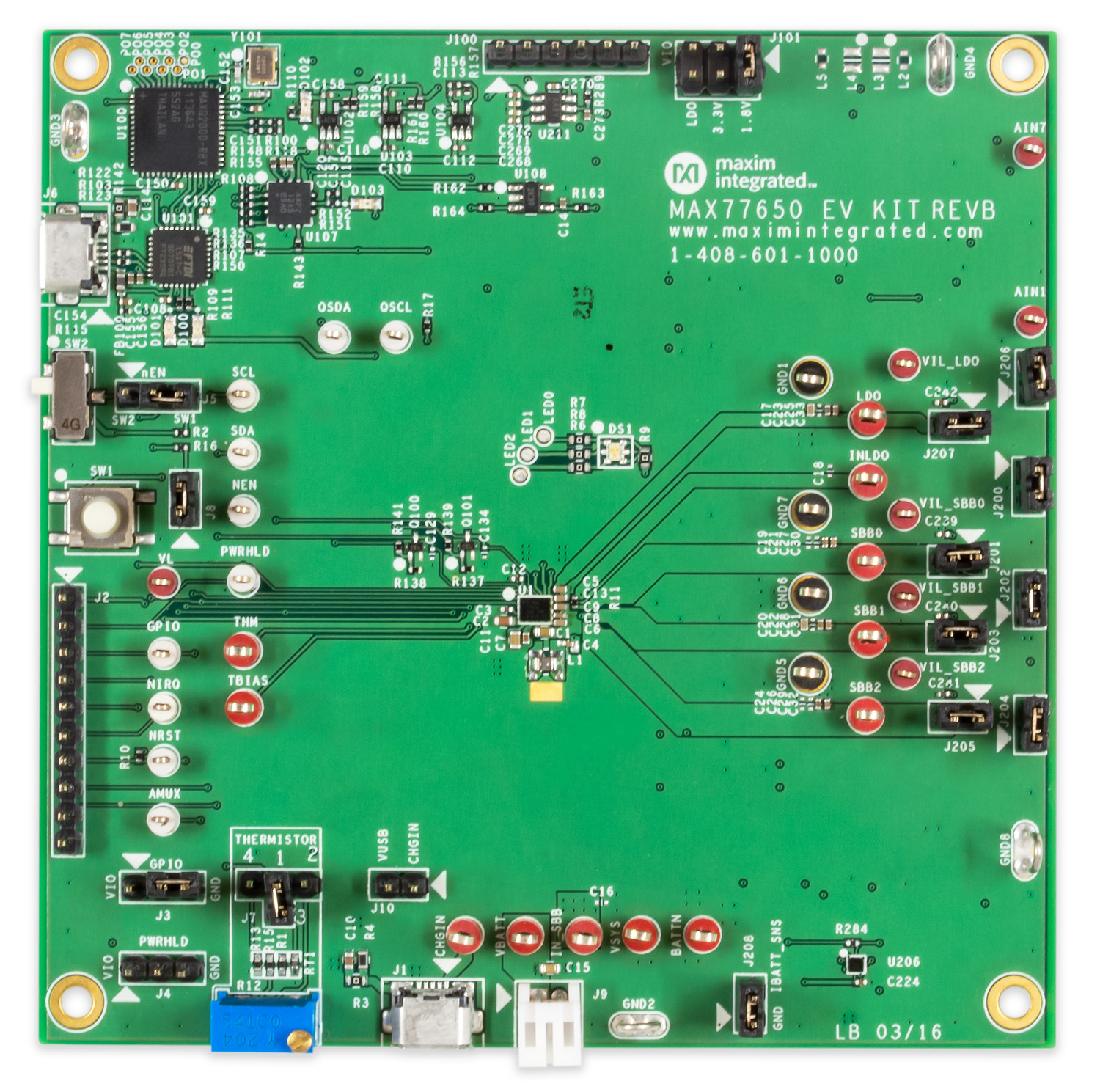
C’est d’ailleurs de Renesas, connu pour ses microcontrôleurs, que vient le circuit que nous examinerons.
Le schéma fonctionnel (fig. 9) du BMS intégré ISL94212 réunit sur la gauche les connecteurs pour la masse (en bas) et la borne positive et la tension de la batterie (en haut) ainsi que les nombreux connecteurs pour douze piles au lithium en tout.
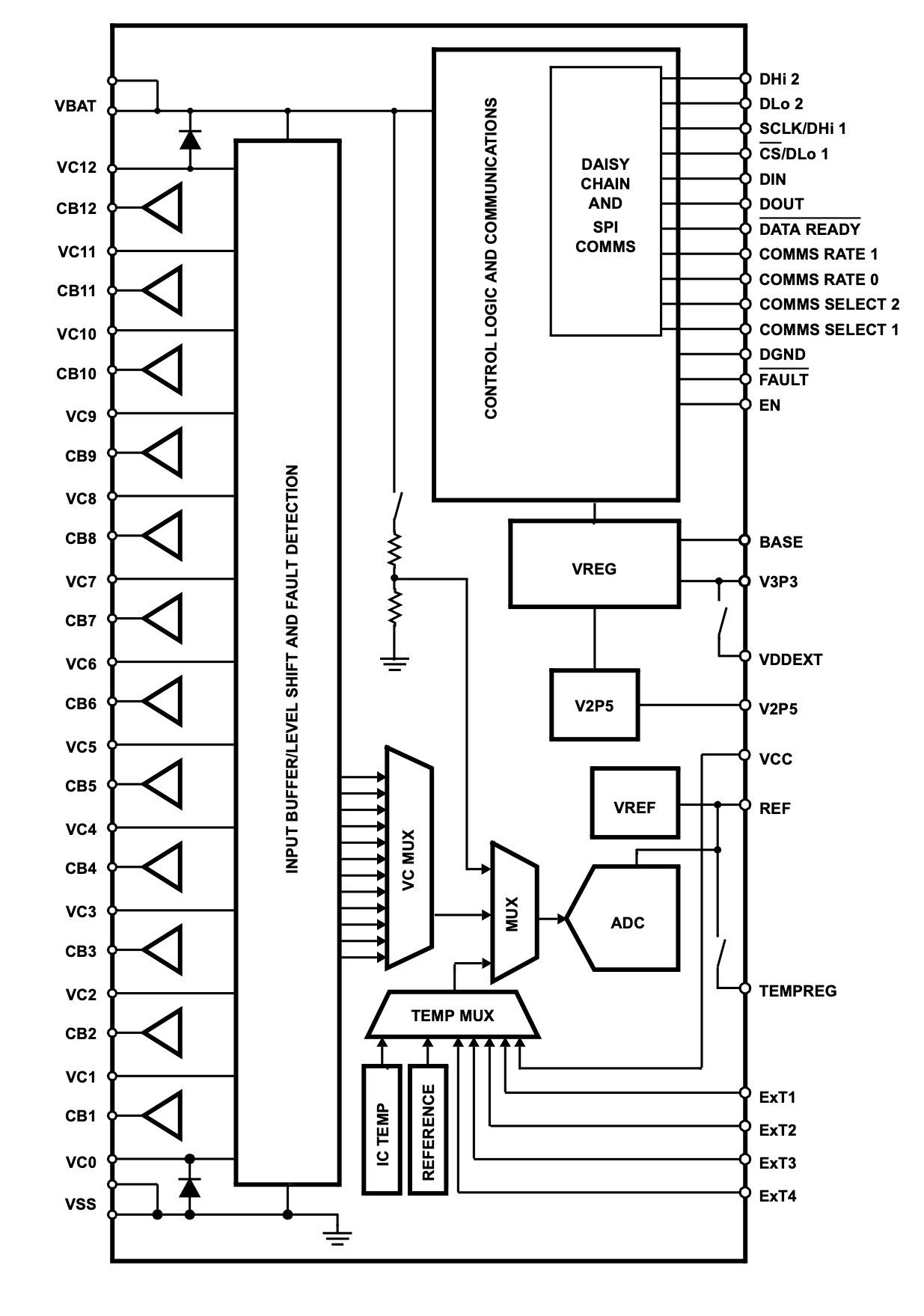
Les tensions proviennent du tampon d’entrée et adaptateur de niveau (Input Buffer / Level Shifter) via un commutateur (VC MUX) et un autre sélecteur (MUX) vers un convertisseur A/N. En outre, on remarque des tensions de référence, des unités thermométriques, etc., le circuit de surveillance de la TFD et bien sûr le plus important, le bloc numérique de commande et de communication (Control Logic and Communications).
Le circuit de base de l'application (fig. 10) montre le circuit intégré en détail.
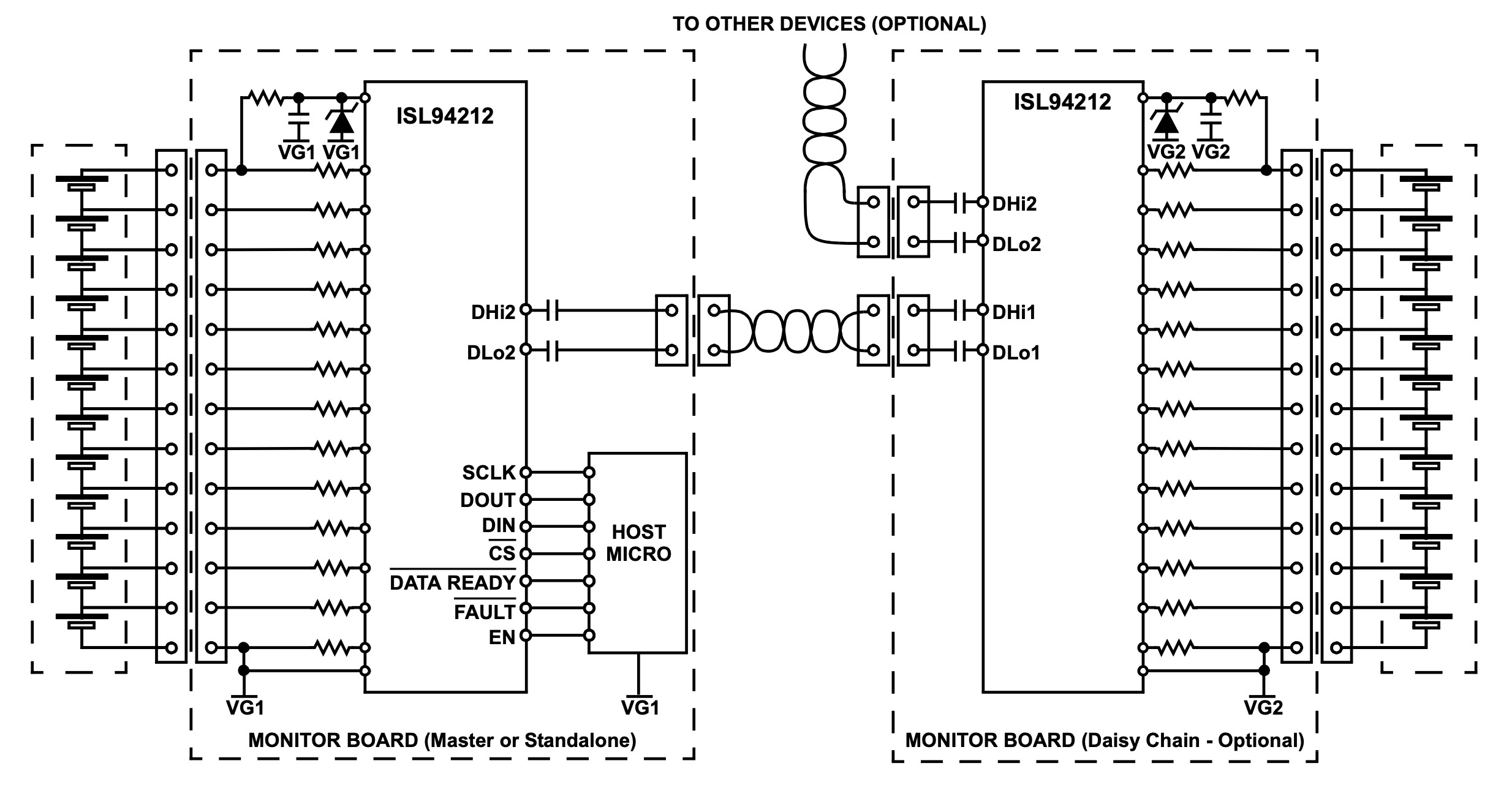
À gauche, la connexion des cellules, et à droite du circuit intégré ISL94212 de gauche, un microcontrôleur qui commande l'ensemble du BMS via une interface numérique. Si vous souhaitez gérer plus de 12 cellules, il faudra des modules supplémentaires, avec un ISL94212 pour chacun. Les modules sont couplés en série : il y a donc deux broches DHi et DLo deux fois par circuit intégré (numérotés 1 et 2). En raison des tensions élevées de ces chaînes de modules, les interfaces série ne sont pas couplées directement, mais par des condensateurs à faible capacité.
Le circuit intégré assure non seulement la surveillance de nombreuses cellules, mais aussi l'équilibrage nécessaire. Le principe de connexion d'une résistance de charge (à l'extrême gauche) à chaque cellule par un MOSFET de faible puissance (fig. 11) est commandé par la sortie CBX correspondante du circuit intégré.

afin de connecter une résistance de charge en parallèle sur chaque cellule.
De cette manière, l'équilibrage peut également être assuré pour des courants d’assez forte intensité. Les détails des nombreuses fonctions du circuit intégré se trouvent dans sa fiche technique.
Pratique
Si vous avez affaire à une batterie au lithium, vous aurez le choix entre trois stratégies : pour les applications simples, il suffit d'acheter une petite carte chinoise, bon marché, assemblée (fig. 5). S’il s’agit d’une batterie plus grande et/ou plus chère, vous avez le choix parmi de nombreux BMS prêts à l'emploi de fabricants établis. Il est possible enfin de trouver une solution sur mesure pour les batteries que vous souhaitez gérer, ce ne sont pas les circuits intégrés appropriés qui manquent. Dans certains cas, il faudra écrire votre propre code pour surveiller et commander la charge des batteries avec précision. Dans tous ces cas, Google finira par vous mettre sur la bonne piste.
180350 VF
Elektor est réputé pour la qualité de son contenu. En voulez-vous davantage ?
► Abonnez-vous maintenant au magazine Elektor et ne manquez plus jamais aucun de ces articles précieux ni aucun de ces projets géniaux.
Discussion (3 commentaire(s))